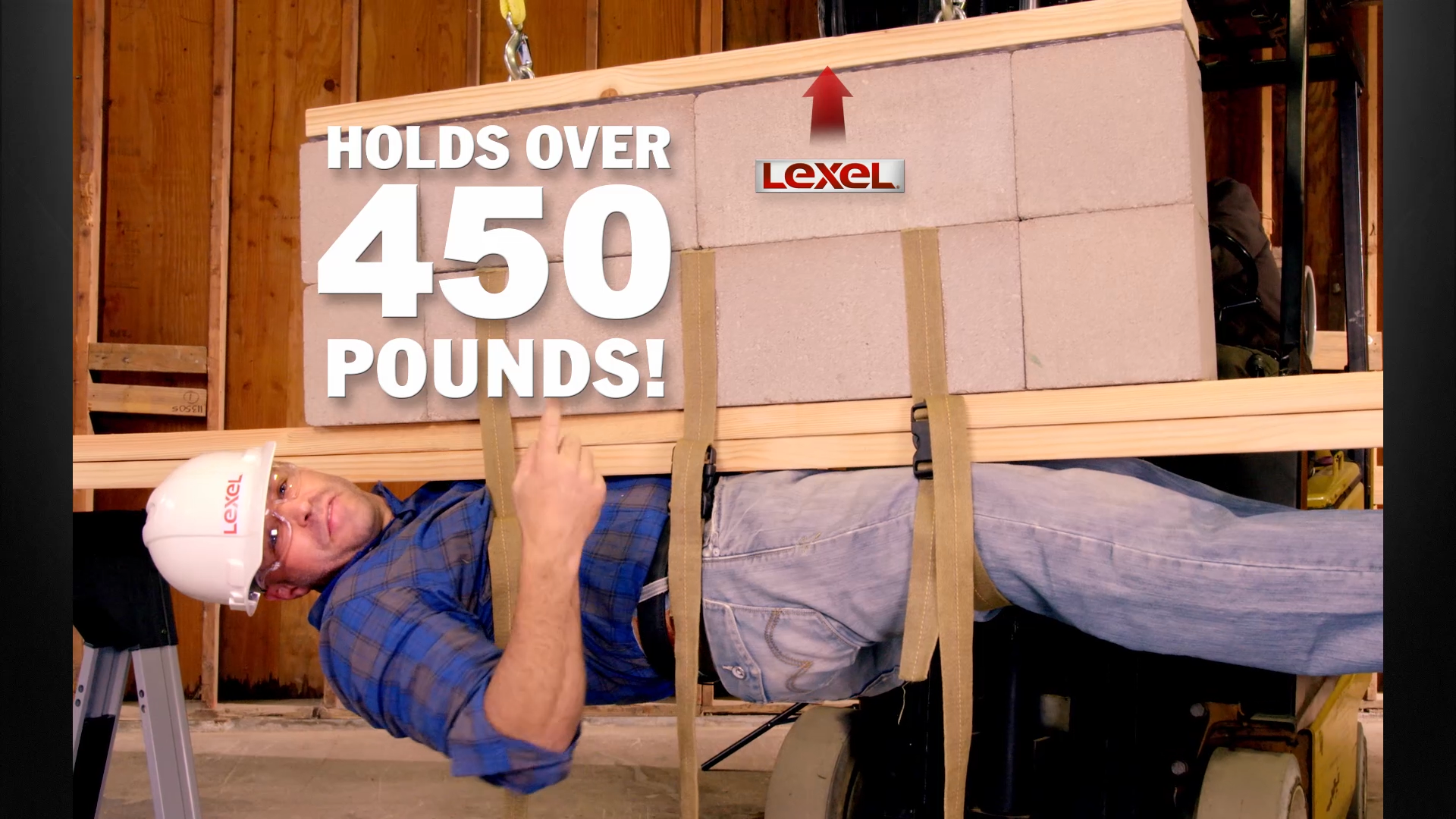
The Best Polymer Sealant for You | Rubber vs Silicone
Are silicone sealants the best answer to caulk performance needs?
It is easy to think so and for understandable reasons.
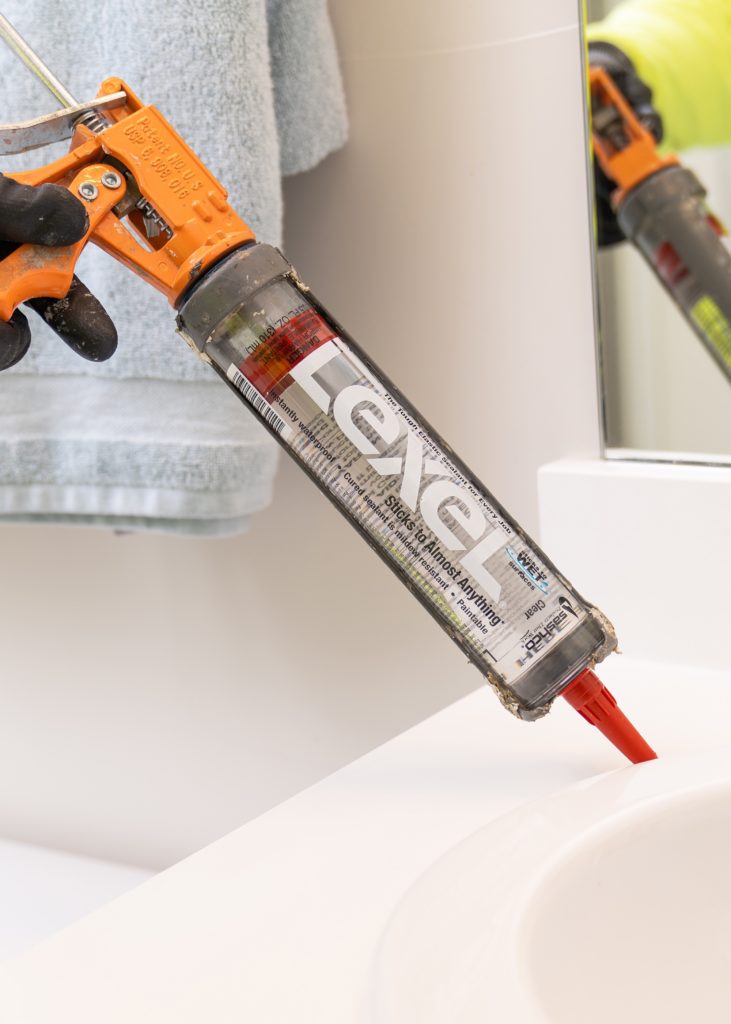
From uses as diverse as medical implants and machinery lubricants to kitchenware and electronic insulation, silicon-based technologies have made their mark on everyday life. That name recognition tends to influence our opinions. So let’s pause and take a look at a competing technology that has also made a significant mark in the construction industry.
That technology is based on copolymer rubbers. For use in sealants, those rubbers are combined with solvents to produce a gel-like consistency and they cure by releasing those solvents. A sister form of these rubbers are also used in construction adhesives.
One example of a copolymer sealant you may be familiar with is Lexel by Sashco. It was the first clear sealant in a clear cartridge. But enough about us.
We’ll compare copolymer rubber and silicone technologies on the following fronts, keeping in mind that formulations can vary widely in performance. You can buy cheap anything. Our comparison will assume top performance sealants of both technologies.
- Clarity
- Adhesion
- Elasticity
- UV Resistance
- Paintability
- Tear Resistance
How Clear is Clear?
Copolymer rubber-based sealants were introduced in the 1980s to offer an alternative to ‘clear’ silicones. Clear is in quotes here because as most everyone knows clear silicones are fairly milky. In fact, for years the cartridges were dubbed ‘translucent’ which was closer to reality. But the newly adopted copolymer rubbers could be made into caulks using clear solvents to yield a truly ‘water-clear’ product. The demand for that difference has shown itself to be quite strong. In addition, silicones will yellow over time, not due to UV exposure (see below) but due to inherent properties in the formula.
Will it Stick?
The first copolymer sealants had very poor adhesion. That frailty was marketed as an advantage in some of the early offerings. “Put it on your storm windows in the fall and pull it off in the spring.” A clever approach to a caulk that, frankly, didn’t stick!
However, by the late ’80s that problem was solved, in spades. Today’s copolymer sealants have excellent adhesion to a variety of surfaces, some traditionally difficult like PVC. Silicones have excellent adhesion, especially to glass and metals. Yet you need to be wary of matching the type of silicone to the substrate. We’ve all opened a silicone cartridge and noticed that sharp vinegar smell. That type of silicone produces acid and will tend to eat concrete rather than stick to it. Just know which silicone technology you are using and which surfaces it adheres to best.
Stretching a Point
Why are silicones what we think of as almost the definition of rubber? To satisfy our expectations of a ‘real’ rubber must stretch, yes, but even more importantly it must recover to its original shape. If rubbers don’t recover they are chewing gum, not rubber. Silicones are legendary in stretching and recovering nearly 100%.
Copolymer rubber sealants also stretch, even more than silicones, and recover well, although in a different way. One of the downsides of silicone recovery (nearly instant when force is released) is that silicone maintains its tension in a stretched joint. Think of stretching a rubber band that continues to pull against you as long as you have it stretched out. Just like your arms will get tired, so will the adhesive bond that has to fight against the stretch. Eventually, something has to give.
Co-polymer rubber sealants have the ability to relax when stretched. When you stretch these out the tension begins to reduce through time relieving the pull against the adhesive bond.
Their Day in the Sun
Even in colder climates, exterior sealants spend much of their life under harsh UV rays. Anyone who has ever slathered on sunscreen knows the sun can be a tough customer. This, so to speak, is where silicone really shines.
Silicone sealants can withstand mega UV and still remain lively and rubbery. The copolymer rubbers will deteriorate over time. But it is a fairly long time. For example, you could expect a rooftop installation in high-altitude and sunny Denver to last 15 years. By then you would see some crazing and yellowness on the surface. If it is painted, double that life span.
Paint it Now or Paint it Later
If you are caulking against a painted surface, chances are that surface will eventually need re-painting. If you have run silicone sealant on it you have also just run out of luck. Most contractors know that paint, whether water or oil-based, just won’t stick to silicone. Many a DIYer has found that out the hard way.
Oil-based paints can appear to cover the silicone but when they dry, they flake off like a rattler shedding skin. Silicones will also leach plasticizers and interfere with paint adhesion to porous substrates such as siding.
Copolymers by contrast take paint well and as mentioned above, painting can actually extend their lifespan. However, there is caution when painting copolymers with oil-based paints. Allow the sealant to cure for an extended 10-14 day period. These sealants cure by solvent release and even a small amount toward the end of cure can interfere with the cure time of oil-based paints. With that in mind, paint away!
That Tears me Up
Actually, we’re talking about torn caulking but it could bring a tear to your eye. You may have observed that silicone sealants tend to tear easily, One little nick in the bead and a tear can run down them like a zipper.
It’s difficult to put a nick or small tear in a copolymer rubber sealant. They have tremendous tear resistance. However, if you can do it then stretch the bead out a few 100% and watch. The tear will not propagate.
What Does it All Mean?
If you have the habit of reaching for the silicone remember to give the copolymer rubber-based sealants a try. They have several performance properties that make them a more fool-proof choice. Both technologies have their best uses and are viable choices.